Nicholas Benson
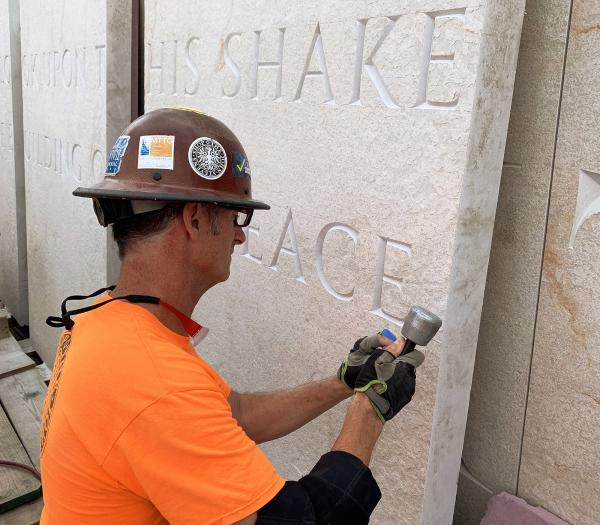
Photo courtesy of Nick Benson
Bio
Nicholas Benson is a third-generation stone carver who today oversees a family shop that was established in 1705, one of the longest continuously running trade businesses in the United States. Over the past three centuries, the John Stephens Shop has produced headstones for New England gravesites and its skilled artisans have designed and inscribed calligraphy on buildings and stone monuments. As with many trade crafts, Benson learned through a journeyman and apprentice system. In addition, he traveled to Basel, Switzerland, to study type design and calligraphy with European masters. Renowned for its flowing sculptural qualities and precise design, the work of Nick Benson and his father can be seen on the Maya Lin-designed Civil Rights Memorial in Montgomery, Alabama; the Poet's Corner in the Cathedral of St. John the Divine in New York; and the National Gallery of Art, the Kennedy Center, the National Cathedral, and the World War II Memorial in Washington, DC. Recently, Benson himself completed the work on the Georgia O'Keefe Museum in Santa Fe. The work of the Benson family was documented in the film Final Marks and in 2001 Benson was featured in the "Masters of the Building Arts" program of the Smithsonian Folklife Festival.
Interview with Mary Eckstein
NEA: First of all, congratulations on your award. How did you feel when you heard the news?
MR. BENSON: I was really amazed. I knew nothing about the award. I went online and took a look at it and thought, "Wow, this is quite something." It really bowled me over.
NEA: Tell me a little bit about how you got into stone carving, and learning the design and lettering process.
MR. BENSON: My father, John Everett Benson, studied with my grandfather John Howard Benson and eventually took over the business, so I grew up with it. It all sort of seeped in via osmosis through my whole youth. My father taught me everything he knew about doing the work and I was a quick study. Even before I went off to college he was doing all of the layout work and I was carving finish work. The interesting thing is when I got off to college, I got a much better perspective of the business and understood what a unique place it is. That's when I started seriously considering getting involved full-time. I'd always had a good eye for letter form and good design and things like that, and when I started studying art in college, it became all the more obvious. So I decided to take it on full-time, realizing that I was not only good at it but really enjoyed it.
NEA : What are the most challenging aspects of your work?
MR. BENSON: The calligraphic end in the design, the lettering, is the most demanding part. The actual physical stone carving is a skill that pretty much anyone can learn. Of course, there are different levels of expertise, very subtle refinements of that craft. There are only a handful of carvers who are of a particular ability. When I came back to the shop after college and studying design in art school, I started getting into the calligraphy and the letter form. And once you get into it and work hard on it, it really is the most rewarding work. To see the entire thing, both the design and the carving come together in a nice unified way is very rewarding.
The standards here at the shop are sort of ridiculously high -- most people would think they're maniacal. I'm very serious about finish work and the whole process. But that's what makes for a very high quality of product.
NEA: Tell me a little bit about the design process? What guides your aesthetic?
MR. BENSON: When my grandfather bought the John Stevens Shop back in 1926, the Stevens family had been running the business pretty much like any other monument company in America. They had a sandblasting booth, didn't really do much hand carving work. But my grandfather was really inspired by the work of the first three Stevens -- John I, John II, and John III -- who were colonial-style carvers. He decided to go right back to that approach because he felt it yielded the best results. The direction I've taken the shop follows the lines of his aesthetic, which was not only colonial style but, more importantly focused on the origin of letter form, the Roman classical form. As a result he picked up a broad-edge brush and began painting letters very much the way the Romans painted letters before they inscribed them. I prescribe to that same approach. I use the broad-edge brush and the mallet and chisel exactly like he did. I followed what he believed was the best way to design. The ultimate refinement of that classical capital Roman alphabet is so important here at the shop that it commands a lot of the design.
The execution of any given inscription is always a challenge. I try to bring something new to it each time I pick up the brush. The thing to keep in mind is that the way the ornament is designed and executed ties in directly with whatever type of character that you design. You design the ornament so that it has aspects of weight and occupies a certain amount of space that ties in nicely to the letter form. My grandfather's whole idea was when you have a particular idea, you have to understand the tools with which you're going to make this idea come to life and the materials that you're going to be using. The combination of the idea, the tools, and the understanding of the material produces this fourth thing, which is the net result.
NEA: Has the stone you use changed over the years?
MR. BENSON: Yes. We use a dark gray slate, what is sometimes referred to as black slate -- that comes from Virginia. My grandfather used a slate that came from Maine. Those two materials are quite a bit different, but the result is very much the same. I'm also using an English slate now, which kind of ties back into the Maine slate a little bit. Then there are the different granites.
Architects tend to go through phases of what types of stone attracts their attention, which then become popular among the building types. A granite called Dakota Mahogany was very popular in the ‘90s. Right now Deer Isle granite and Kershaw are very popular. Mount Airy is also very popular. You see these materials in buildings all over the U.S. and we have to adjust accordingly. The letter form I used for the National World War II Memorial I designed specifically for the Kershaw granite they decided to use.
NEA: What's it like running an historic shop?
MR. BENSON: It's a small business, just me and a couple of guys I have working with me. That's it. I'm like any other small business owner, running around trying to keep things rolling on a day-to-day basis, doing clerical things, putting out all kinds of fires, and all of that.
Every now and then I'll flip through a drawer or a file and the legacy will really hit me. I'll pick up, say, a file my grandfather started with Mrs. So and So back in 1920 and see the work my father did for that family then, and now the family's come back to me. That legacy is really impressive to me. And even though I'm the owner/operator here, I still feel very much like I am just the custodian. It's such a funny little business. It's not this grand institution, but it's such a long and interesting legacy.
Our shop is just one small building on Thames Street here in Newport, the kind of place you'd drive right by, not give a second look. I don't like to feel as though the place is so historic that I can't change it to suit the need. I'm not really interested in continuing "ye olde shoppe" and turning it into a museum. It's not a museum - it's a working and functioning business that has a lot of merit in contemporary design. It's important to keep the business topical.
NEA: Have there been innovations to stone carving, or has it stayed pretty much the way it was?
MR. BENSON: There have been some substantial changes over the years that have had a very strong impact on the shop. Sand blasting has always had an impact on the shop -- that was the method devised to incise lettering into stone. You place a rubber mat on the stone, then take away the parts where the letter forms will end up being incised into the stone. You blast sand at high pressure and it simply etches these letters into the stone. That's the way almost all lettering is cut in stone today. What we do - the hand-carved V cut -- represents a particular skill that is not popular in America at all. Sand blasting does not leave a particularly attractive cut. The V cut is vastly superior aesthetically. If you look at a V cut letter and a sand blasted letter, there's no comparison. The V cut is just a much prettier form. That's the way in which the Romans did it. It's how the classical Roman cap that everyone takes for granted came about.
The technological development that has had the most significant impact on the shop is the personal computer. Everyone who buys a computer now thinks they're a designer because they have a whole book of fonts that they can grab and design programs where they can pop in photographs and lettering and so forth. This is how architects work now -- everything is done in the computer using CAD. And there's a very tight relationship between graphic designers and architects nowadays: an architect will design something in CAD and then the first person they go to to develop inscriptional work is a graphic designer, because they also work with the computer. And that's what I'm having the most trouble dealing with today. I keep coming up against jobs where they say, "We'd love you to carve this inscription. Here's what the graphic designer has designed." And I say, "You know, I'm not really interested in what the graphic designer has done. They're designing for two dimensions." They don't know everything that goes into carving letters in stone and what works with particular materials and the way in which you have to deal with letter weight in certain material. There's so much that goes into it that graphics people just have no idea about.
Please don't misunderstand me. I'm not damning graphic designers. All I'm saying is that there are certain aspects of design when it comes to stone work that I understand that the graphics folks don't. There are some amazing graphic designers out there who were calligraphers and things like that first. But the younger set has dealt solely with graphic design in the digital realm.
NEA: Are they receptive to your ideas?
MR. BENSON: I did a very interesting job at Yale University recently. They refurbished the Yale University Art Gallery, a Louis Kahn Building that was in really tough shape. They spent millions of dollars to spruce the place up. There's a large run of slate that runs along the sidewalk next to the building that has a large incised inscription which reads "Yale University Art Gallery." A large graphic design firm did all of the signage for the building. Then they looked at the slate and said, "Oh, we're going to use the Gotham typeface," a graphic design that's very popular in the graphics world right now. I said, "Absolutely not. You cannot use that typeface in this application. It's going to be brutal at 5 1/2 inches in this slate to V cut this thing. The weight of the thing will be absolutely overpowering and it will look ridiculous." So I said, "Let's draw something up." I worked directly with the head of the firm and he understood from the get-go that it could be something really interesting. I designed a letter for that particular run of slate, digitized it, and we hand cut it. It turned out beautifully. That's exactly the type of process I'm hoping I'll do a lot more of as people get more and more familiar with the graphics work and their understanding of it grows, I think there will definitely be a larger need for a higher standard in site-specific work.
NEA: What has been your greatest source of pride or happiness as a stone carver?
MR. BENSON: It's really nice to look back on a body of work and realize that you're leaving behind something a little bit more powerful than just a paper trail. You have this physical evidence of your existence. I think this is true for any artisan and/or artist. It's really interesting to look at the the work and see how it evolved, and to draw the connections between pieces. And it's a real source of pride when I look at these things and I can see how I really did do a nice job on this one particular thing. That there were particular issues and complications that came up and and I had to do this and I had to do that and in the end I wound up with something that's really quite successful. That makes me happy.