Ron Poast
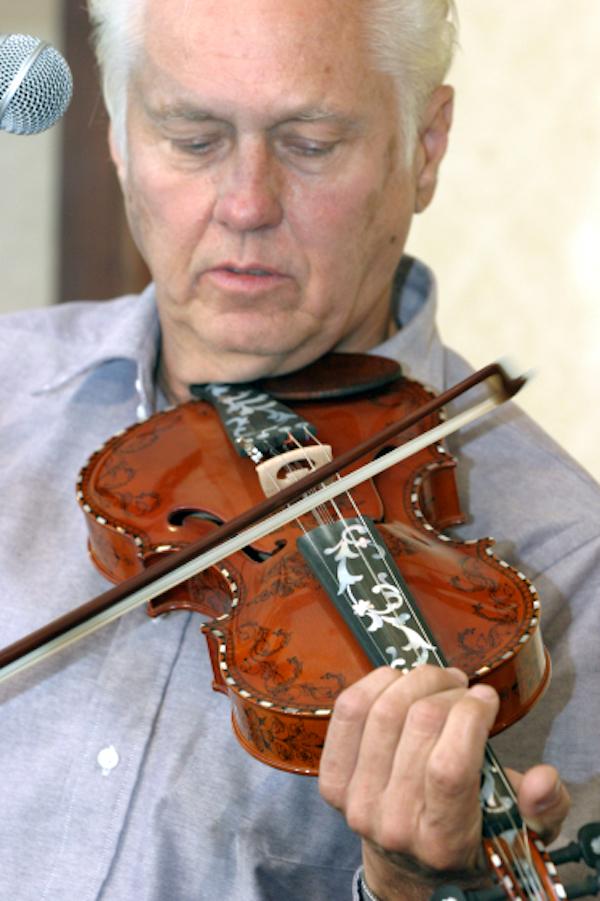
Photo courtesy of the artist
Bio
Born in rural southwestern Wisconsin to Norwegian American parents, Ron Poast grew up surrounded by a variety of regional musical traditions. His grandfathers on both sides and his father were fiddlers, playing Norwegian styles as well as rural country music popular at the time. Poast initially learned to make fine banjos and guitars but it was his interest in and skill at making the hardingfele or Hardanger fiddle, recognized as the national instrument of Norway, that brought him nationwide acclaim.
The elaborately decorated instrument with a dragonhead scroll has four bowed violin strings and four or five sympathetic understrings that produce a unique droning sound. As one of less than a half-dozen makers of hardanger fiddles in the United States, his instruments are in high demand. Poast has exhibited his craftsmanship at the Smithsonian Folklife Festival and has participated in cultural exchange programs with Japan, in addition to offering workshops at the annual meetings of the Hardanger Fiddle Association of America.
In 1992, Poast was nominated by then Governor Tommy Thompson for the National Living Treasure of the United States Award and that year was also inducted into the Wisconsin State Strings Museum Hall of Fame as Master Luthier of the Year. A photograph of one of his fiddles graced the cover of the 1992-93 State of Wisconsin telephone directory.
Interview with Mary Eckstein
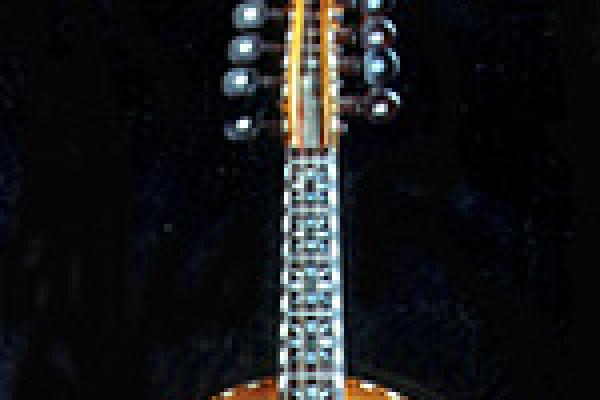
NEA: First of all, I want to congratulate you on the award. Could you talk a little about how you felt when you heard the news.
Poast: When I got the call from Mr. Bergey, I was very happy and very surprised. I knew that I had been nominated but didn't really think it would ever go through. But it did. It's really a great honor.
NEA: You grew up in a musical family. Could speak about that and what influence that had on you?
Poast: Both my grandfathers and my father played violin. My mother can play just about anything she gets a hold of. My uncle played dobro guitar. I grew up on a farm and Sunday was, of course, a day of rest, so we would go to visit the relatives or friends or they would come to our place. We always took our instruments and played, which was a very common thing back then. There wasn't TV and all that kind of stuff like there is nowadays.
I don't know where the violin-building part of it came in but I've always liked to work with my hands. I was interested in the music. But I started out actually building banjoes.
I went into a town not too far away from here, Madison, and bought a cheap banjo and played on it for a little while. Since I liked working with my hands and doing woodwork, I decided could build a better banjo than that one. So I did and it didn't take long. Some of my friends saw it and pretty soon I was building instruments for them. And it sort of evolved into making the Hardanger fiddles and regular violins and guitars and mandolins, and a lot of the smaller instruments.
NEA: Were there other fiddle makers in the community?
Poast: No, not at all. I had nobody to go to, no way to get any instruction. I'm basically self-taught.
NEA: And how did you first hear about the Hardanger fiddle?
Poast: My mother always talked about a "very fancy violin" that her brother - my uncle - had when they were young. They didn't really know what it was. The story goes that at one time he needed some money, so he just sold the instrument and it got away from the family. I don't know who made it but it turned out it was a Hardanger fiddle.
Then one day I was up in a town about ten miles south of here, and I saw two very fancy looking violins in a storefront. I knew right that was what my mother was talking about. I went in and asked about them, and it turned out they were Hardanger fiddles.
We found out that the Vesterheim Museum here in Iowa had Hardanger fiddles on display so we went up to look at them. They were extremely nice to us ® took the fiddles out of the display and gave us a room and told us, "Take all the pictures you want, all of the measurements you want." By the time we were on the way home we were building Hardanger fiddles.
NEA: Now, I know there are a lot of unique aspects to the Hardanger fiddle. Can you talk about those and how it's different from a conventional violin?
Poast: The first thing is the decoration. A violin isn't normally as highly decorated. The Harangers instruments have mother of pearl in the fingerboard and the tailpiece, and sometimes around the top and bottom of the body.
Then there are the line drawings. We call it "rosing," the painting of the roses. It is like a pen and ink type of a drawing and is usually on the top and sides and the back of the instrument.
Secondly, what we call the F-hole - on the top or the belly of the instrument - is carved quite differently than a violin. That's a sound hole and is a very prominent feature. Looking at a violin from the front you can see inside of the instrument. On a Hardanger fiddle you can't. You have to look in from the side of the F hole. I can't really say that it makes a lot of difference in tone but it's a difficult thing to do and it shows how good a craftsman you are.
The scale - the distance from what we call the nut up by the tuners to the bridge - is usually a little shorter than a violin. Violin designs are fairly locked in but Hardanger fiddle designs are not. The Hardanger fiddles were made by a lot of individuals years ago so there's quite a bit of variation from one instrument to another. I see a lot of them here for repairs so I see a lot of those variations. You will see some fairly large ones almost the size of a violin and you'll see some very small ones.
The waist or the center part where the center bouts are will be quite narrow. The box, the body, is a more squarish feature than on a violin. That's a distinguishing feature.
The Hardanger also has a different number of strings. The first Hardanger that we know of is in a museum in Norway ® it was built in the 1650s. On that instrument there are four strings on top like a violin that you play with a bow, and two strings that run from the tailpiece through the bridge underneath the fingerboard and up to the peg box, and two extra tuners. So we ended up with a six string instrument.
We still only play on the top four as with all of the Hardanger fiddles, even today. They tell me that they've added one string every 100 years, so I think most of the modern makers are using five strings underneath. Four on top and five underneath, making a nine string instrument. Things are getting pretty crowded down there now so I don't know what we're going to do in the next 100 years.
NEA: I understand that it produces a unique sound. Is that because of the five strings on the bottom?
Poast: That's one of the reasons, yes. When you play a note on the top four strings, any note, if any of the under strings are tuned at that same note or an octave of that note, sympathetic vibration will excite that string and it will produce a tone. When you move to the next note on the top four strings there's nothing to dampen that one that was excited so the sound stays there longer and gives the instrument what we call more sustain, and that's part of the sound.
The tuning of the instrument is part of the sound, too. I've been told that a hundred and eight different tunings have been documented. The most common violin tuning is E-A-D-G. Well, on a Hardanger fiddle all of the strings are up one full tone. And then the bottom G string would be up another full tone. So in true music that would be all the way up to a B. So we have starting with the treble an F sharp, a B, an E and a B. Now that's more of what we call a singing tone. It's higher pitched. The instrument itself is built a little lighter, more fragile than a violin so this all works out but, like I say, this is only what we consider the most common tuning. So many other tunings are used.
The bottom under strings are tuned in a relationship to the top ones. Every time the top strings are changed, the bottom are also changed, but not always in the same relationship. It does get a little confusing.
Another difference is that the bridge of a Hardanger is flatter than a violin. When you play on a violin you can play a single string quite easily. It's a little harder to play on two strings, what are called double stops. Because of the flatter bridge on a Hardanger fiddle, it's easier to play on two but a little harder to play on one.
So if you use a bow that doesn't have very much arch or spine to it and the hair is not real tight, you can actually play on three strings at a time, so you can get a nice chord.
The peg box is longer than a violin because of the five tuning pegs there. Most of the Hardanger fiddles will have some type of a mythical dragon for the head on the instrument where on a violin it would have a scroll design. We usually put in the tongue and the teeth, and there'll be some drawings, the eyes, and on the ones I make I usually put some freckles on. Of course, they don't look so vicious then.
NEA: The dragon is from Norwegian mythology?
Poast: Yes, that's a Norwegian design. What I'm doing, I'm not changing the design - I'm just continuing. I tell people that I'm staying within the realm of tradition. You can vary somewhat - even the old ones did that. And you can put some of yourself into it, too. But you don't want to get too far away from what a Hardanger fiddle really is.
NEA: Where do you get your materials?
Poast: All over. I get some locally here. We even go out and saw down our own trees and dry our own wood. I also purchase wood from other places. I use ebony from Africa and Sri Lanka on the fingerboards which I buy from importers. We can get mother-of-pearl out of the Mississippi river here but that's not the top quality stuff. The best comes from Australia and New Zealand. I also buy that from importers.
NEA: You're one of the few Hardanger fiddle makers in the United States, isn't that right?
Poast: I only know of three. If I veer off of this realm of tradition and those other two people follow, things are not going to be what they really should be. One is a fellow in Montana and the other is in Washington State, both of whom were my students. They're the only ones that I know of in the U.S. that are actively doing this. So we have to stay pretty on the, you know, very close to the straight and narrow, and all three of us do.
There are several instrument makers in Norway. Of course, the Hardanger fiddle is considered the national instrument of Norway. So over here in the U.S., with just the three of us that I know of, we've got to be kind of careful to make sure we do everything as right as possible or the Norwegians are going to be over here really mad at us.
NEA: Are there any other challenges to continuing the tradition of fiddle making?
Poast: If we don't teach the younger people how to build the instruments and how to play them, the whole thing is going to be gone. When I first started, I figured I probably wouldn't build more than 50 instruments in my whole life. Well, I'm way beyond that now. There are many of them here locally here I never knew existed until they were brought into my shop for repair. So if we can keep this thing going and increase the number it would be great. It's a beautiful instrument and has a beautiful tone. It's something that we really don't want to lose.
NEA: I would imagine that showing the instrument to someone who has seen one must be quite an experience?
Poast: It really is. The first thing they notice, of course, is the beauty of the instrument. We put on a display to show them how we make them, all the different individual parts. We start with the raw wood and lay out a display and proceed in steps until we get up to a finished instrument.
But the most important thing is the tone. Once you've finished showing how one is built then almost everybody wants to hear you play a little tune. Well, I'm not a professional musician but I can scratch out a few tunes so everybody seems to be satisfied.
NEA: And how long does it take you to make a Hardanger fiddle? You said you had made over 50 by far. How many would you say?
Poast: I spend well over 200 hours per instrument on the nicest Hardanger fiddles I make, So with the time for the finish to dry and the glue to dry and everything else, it take about three months before I can finish one. I try to make parts ahead of time if I get any extra time. I'll make extra fingerboards or maybe the tops and backs, so when I get an order the lead time isn't so long. Right now lead time is between three and four years - a lot of people who don't really like to wait that long.